The Quest for Operational Excellence
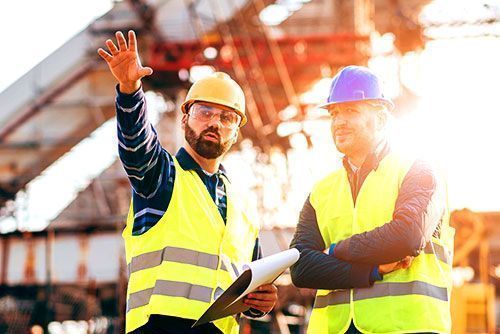
According to executives, 40% of a strategy’s potential value is lost due to breakdowns in execution.
As seen in other industries, there is a long-standing gap between strategy and execution, or process and practice. This gap possesses significant risks when it comes to the “3D” (difficult, dirty and dangerous) industries and their initiatives around safety. And it is this gap that continues to hinder their quest for true operational excellence.
Take BP and the Deepwater Horizon Oil Spill for example. The question is not if BP had safety and operational processes in place (based on best practices, legal requirements and industry regulations). They did. When it comes to the success or failure of these processes, the question is, were those processes executed? Where was the gap between process and practice? How big was it? And where was the breakdown between BP’s strategy of safety and the day-to-day execution?
Reported in the NY Times, Jordan Barab, deputy assistant secretary of labor for OSHA stated BP “need(s) to take their intentions and apply them much more effectively on the ground, where the hazards actually lie.” Forbes notes, “At the same time, these technologies and underlying processes are run by people under pressure to deliver economic performance, under deadlines, where time costs money and shortcuts can potentially save millions…the culture of safety is less strong than the imperative to meet deadlines….” There was obviously a gap between process and practice. One that cost $61.6 billion, catastrophic environmental damage and irreparable loss of human life.
Clearly, there is more to be realized and improvements to be made when it comes to operations risk and safety management. To date, most investments focus on the equipment, process and environmental factors of mitigating risk and increasing operational safety. Yet, as highlighted by BP, organizations are realizing that the workforce plays an undeniable part in ensuring successful execution and creating a true culture of safety.
Fostering and maintaining a sustainable culture of safety is an operational imperative. There are three high-level facets in creating safety from within:
- Capture and communicate operational intelligence from within and across your entire workforce. This includes contractors, service providers, seconded employees, etc. Deliver these critical, proactive real-time insights in an actionable method, providing the information to the relevant workers at the right time to make the most informed decisions.
- Empower workers by making operations risk and safety a personal responsibility. Create a shared responsibility for your organization’s safety agenda through two-way communication allowing workers to not only receive information but submit ground-level insight on concerns, risks and potential failures. Enable the workforce to make the most intelligent operational decisions with less risk.
- Enhance shareholder value through reducing failures and improving safety across the business. “The fire not only destroyed BP’s physical property and caused casualties, but also destroyed shareholder wealth” (MarketRealist). Achieving sustainable operational excellence is directly linked to shareholder value as well as business performance and success.
Creating a true culture of safety is an operational requirement. It’s importance and strategies for fostering and maintaining this type of cultural shift are a few of the topics Questback VP of Sales, Americas, Justin Flanagan will cover in his presentation, Ensuring Operational Safety from Within, this week at PowerGen 2017, the world’s largest power generation event.
“Despite advances in technology, best practices, processes and procedures, we still lose more than $3 trillion annually due to failures and incidents,” states Flanagan. “The missing piece – bringing technology, process and external factors together – is the workforce.” Ensuring Operational Safety from Within delves into that missing piece – the workforce – and how organizations can leverage a workforce-centric strategy to generate tangible improvements and business results.